How Steel is Made: From Iron Ore to Metal
Steel is a fundamental material that forms the backbone of modern construction, transportation, and various industries. However, the journey from raw iron ore to the finished metal is complex and fascinating. In this article, we’ll break down the steelmaking process, including how metallic iron is derived from iron ore, the chemistry behind the process, and why it’s critical for our industrial world. If you're seeking insights into the practices of the best steel manufacturing company in India, understanding this process is key to appreciating the quality and innovation behind their production.
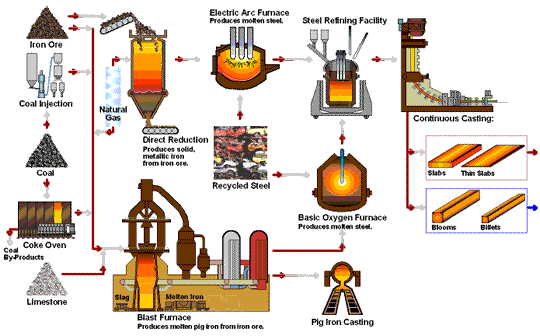
Transformation of iron ore into steel.
Understanding Iron: The Core Element of Steel
Iron, symbolized as Fe on the periodic table, is the fourth most abundant element on Earth. It’s essential in manufacturing due to its strength, versatility, and malleability. But iron does not exist in its pure metallic form in nature. Instead, it’s found in iron ores, rocks that contain high concentrations of iron minerals mixed with other elements. The iron in these ores is primarily combined with oxygen, creating iron oxides.
The most common iron ores include:
- Hematite (Fe₂O₃)
- Magnetite (Fe₃O₄)
- Limonite (FeO(OH)·nH₂O)
- Siderite (FeCO₃)
These ores serve as the foundation of steel, and to convert them into usable iron, it’s essential to remove the oxygen atoms—a process requiring heat and a reducing agent.
Iron Extraction: Transforming Ore into Metallic Iron
The iron extraction process begins with mining iron ore from large open pits, which is then transported to steel plants. The ore undergoes smelting, where it is heated to around 1,700°C in a blast furnace with coke and limestone. This high-temperature process removes oxygen from the ore, resulting in metallic iron and carbon dioxide through a reduction reaction: Fe₂O₃ + 3CO → 2Fe + 3CO₂. Additionally, limestone reacts with impurities to form slag, which is removed from the molten iron. This transformation is essential for producing high-quality steel.
Step 1: Mining Iron Ore
The process begins with mining iron ore from the Earth. Mining typically occurs in large, open pits where iron ore is extracted in its raw form and transported to steel plants.
Step 2: Smelting – Heating and Reducing the Ore
Smelting is the primary process that converts iron ore into metallic iron. It involves heating the ore at high temperatures (around 1,700°C or more) to separate iron from its natural impurities, primarily oxygen. Here’s a closer look at the key stages:
- Preparation:The ore is crushed and washed to remove dirt and impurities.
- Blast Furnace Introduction:The prepared ore is loaded into a blast furnace along with coke (a form of carbon made from coal) and limestone. The coke serves as the reducing agent, while limestone helps remove impurities.
- Reduction Reaction:Inside the furnace, oxygen is removed from the ore in a reaction with the coke, producing carbon dioxide and leaving behind metallic iron. This reaction is known as reduction and is fundamental to steelmaking:
Fe2O3+3CO→2Fe+3CO2Fe_2O_3 + 3CO → 2Fe + 3CO_2Fe2O3+3CO→2Fe+3CO2
The high temperatures in the furnace drive this reaction, resulting in molten iron, also known as pig iron. - Slag Formation:The limestone reacts with other impurities in the ore to form a byproduct called slag, which floats on top of the molten iron and is removed periodically.
Refining Iron into Steel
Pig iron obtained from the blast furnace is rich in carbon and brittle, making it unsuitable for most applications. To convert it into steel, the carbon content needs to be adjusted through further refinement.
Basic Oxygen Furnace (BOF) Process
- Molten Iron Transfer: : The molten pig iron is transferred to a Basic Oxygen Furnace.
- Oxygen Injection:Pure oxygen is injected into the furnace at high speed. This step reduces the carbon content, forming carbon monoxide and leaving purer iron behind.
- Alloying:After de-carbonization, elements like chromium, nickel, and manganese can be added to create specific types of steel, such as stainless steel or alloyed steel with specialized properties.
The BOF process produces a high-quality, durable steel used in everything from infrastructure to cars and appliances.
Alternative Steelmaking Methods
While the blast furnace process is the most common, there are alternative methods as well:
Electric Arc Furnance (EAF)
The Electric Arc Furnace (EAF) is used mainly in recycling steel and producing specialty steels. EAF doesn’t rely on raw iron ore but instead melts scrap steel using electrical currents. This method is more sustainable and energy-efficient, making it popular in modern steel recycling.
Direct Reduction Process (DRI)
The Direct Reduction Process uses natural gas rather than coke as the reducing agent, making it a more environmentally friendly alternative. Direct Reduced Iron (DRI) is often used in regions where natural gas is abundant and is ideal for producing high-quality steel with less carbon emissions.
Finishing and Shaping Steel
After refining, the steel undergoes further processes to achieve the desired shape, strength, and surface finish:
- Casting: The liquid steel is poured into molds, forming ingots, slabs, or other shapes.
- Hot and Cooling Rolling: The cast steel is rolled at high temperatures (hot rolling) or at room temperature (cold rolling) to achieve the desired thickness.
- Finishing: Processes like pickling (removing impurities), galvanizing (adding a zinc coating for rust resistance), and tempering (heat treatment for durability) are applied for specific applications.
The Importance of Steel in Modern Life
Steel is integral to countless aspects of life, from construction and infrastructure to automotive manufacturing, aerospace, and electronics. Its strength, flexibility, and recyclability make it the material of choice for long-lasting applications.
Environment Impact and Recycling
Steel production has historically been energy-intensive and a source of carbon emissions. However, modern methods like EAF and DRI are helping reduce its environmental impact. Moreover, steel is 100% recyclable, meaning it can be re-melted and reused repeatedly, conserving natural resources and reducing waste.
Conclusion: The Path from Iron ore to Steel
The process of converting iron ore into steel is a testament to human ingenuity and technological advancements. By removing oxygen from iron ore through heating and reduction and refining the product further, we create steel — a versatile, reliable metal that shapes our daily lives. As the industry embraces more sustainable methods, the future of steel production promises to be both innovative and environmentally conscious.