The Process of Iron Ore Mining: From Earth to Steel
Iron is one of the most important metals in the world, forming the backbone of modern construction, manufacturing, and technology. From the skyscrapers that grace city skylines to the tools and machines that drive industry, iron is ubiquitous. But before it can serve these vital roles, iron ore must first be mined from the earth. In this blog, we will explore the process of iron ore mining, focusing on the predominant method known as open-pit mining, and take you through the stages of extraction and processing.
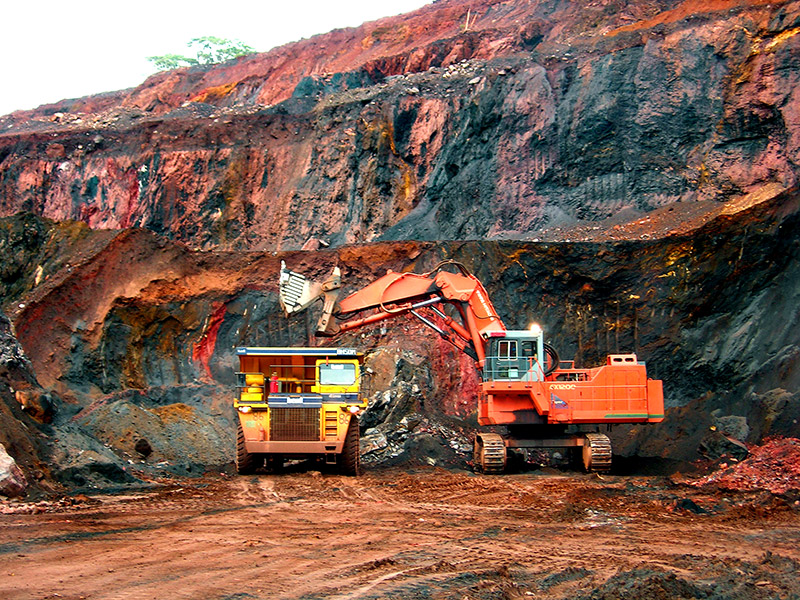
What is Iron Ore?
Iron ore is a natural mineral from which iron (Fe) is extracted. The iron content in iron ore varies, but it is primarily composed of iron oxides such as hematite (Fe₂O₃) and magnetite (Fe₃O₄). The global demand for iron ore has grown steadily, driven by the burgeoning steel industry, which accounts for around 90% of iron ore consumption.
The Importance of Iron Ore Mining
Iron ore mining is crucial as it provides the primary raw material for steel, essential to construction and manufacturing. It significantly boosts local and national economies by generating jobs and supporting industries. Additionally, the high demand for steel in infrastructure projects makes iron ore mining a key driver of urbanization and economic growth, supporting global development.
Iron ore mining is essential for several reasons:
- Raw Material for Steel Production: Iron is a key component of steel, which is vital for construction and manufacturing industries.
- Economic Impact: Mining contributes significantly to local and national economies, providing jobs and supporting related industries.
- Infrastructure Development: The demand for steel in infrastructure projects drives iron ore mining, supporting urbanization and economic growth.
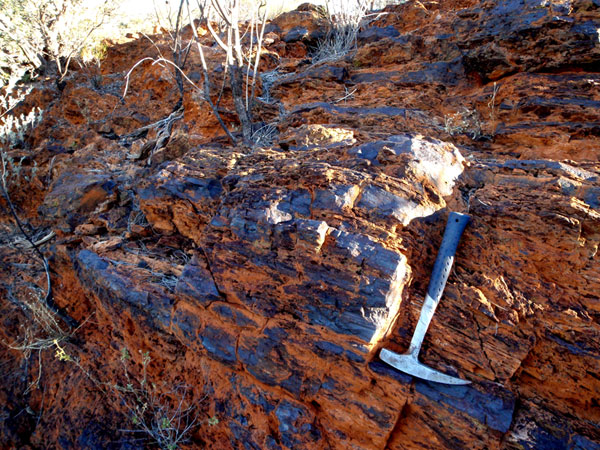
Open-Pit Mining: The Primary Method of Iron Ore Extraction
Open-pit mining, or surface mining, is the primary method for iron ore extraction due to its efficiency and cost-effectiveness. It involves preparing the site, clearing vegetation, and building infrastructure. Overburden is removed to expose ore, followed by drilling, blasting, and excavation. The ore is then transported for processing via trucks, rail, or conveyor belts, depending on the mine's location.
What is Open-Pit Mining?
Open-pit mining, also known as surface mining, is the most common method used to extract iron ore. It involves removing large amounts of soil and rock, called overburden, to access the iron ore deposits beneath the surface. This technique is favored for its efficiency and cost-effectiveness.
Steps in Open-Pit Mining
- Site Preparation: Before mining begins, the site must be prepared. This includes clearing vegetation, building access roads, and setting up infrastructure for the operation.
- Removing Overburden: Heavy machinery such as bulldozers and excavators is used to remove the overburden. This involves stripping away the layers of soil and rock that cover the iron ore deposits.
- Drilling and Blasting: Once the overburden is removed, drilling is conducted to create holes for explosives. Controlled explosives are then used to blast the ore, breaking it into smaller, manageable pieces.
- Excavation: The broken ore is loaded onto haul trucks and transported to the surface for processing. This stage can involve multiple trips to ensure all ore is removed.
- Transporting the Ore: After excavation, the ore is transported to processing plants. Depending on the mine's location, this may involve trucks, rail, or conveyor belts.
Iron Ore Processing: Turning Ore into Iron
Iron ore processing involves four key steps: crushing and grinding to increase surface area, followed by magnetic separation to isolate iron particles from non-iron materials, resulting in iron concentrate. Next, washing and filtration ensure purity by removing impurities, while pelletizing forms the concentrate into transportable pellets for steel production. Each step maximizes iron yield for efficient steelmaking.
Crushing and Grinding
Upon arrival at the processing plant, the iron ore is first crushed and then ground into a fine powder. This step is crucial as it increases the surface area of the ore, making it easier to separate iron from impurities.
Magnetic Separation
Next, the powdered ore is subjected to magnetic separation. This process uses powerful magnets to attract the iron particles while separating non-iron materials such as sand, clay, and other minerals. The result is a concentrated iron product known as iron concentrate.
Washing and Filtration
After magnetic separation, the iron concentrate is washed to remove any remaining impurities. This step ensures the final product is of high purity. The filtered material is then dewatered to eliminate excess water before moving on to the next phase.
Pelletizing
The concentrated iron ore may then be processed into pellets, small balls of iron ore that are easier to transport and use in steel production. Pelletizing involves mixing the iron concentrate with a binder, shaping it into pellets, and then heating them to harden the structure.
The Role of Iron in Steel Production
Once processed, the iron concentrate or pellets are sent to steel mills, where they are combined with coke (a form of carbon) and limestone in a blast furnace. The coke serves as both fuel and a reducing agent, while limestone helps remove impurities as slag.
During the blast furnace process, the iron ore is transformed into molten iron, which can then be further refined and alloyed with other metals to produce various grades of steel. The entire steel-making process is integral to numerous industries, including construction, automotive, and energy.
Environmental Considerations
While iron ore mining is vital for economic development, it also raises environmental concerns. The open-pit mining process can lead to habitat destruction, soil erosion, and pollution of nearby water sources. To mitigate these effects, mining companies are increasingly adopting sustainable practices, such as:
- Rehabilitation: Restoring mined areas by planting trees and vegetation.
- Water Management: Implementing systems to manage water use and prevent contamination.
- Waste Management: Finding ways to reduce waste and recycle materials.
Conclusion
The journey of iron ore from the depths of the earth to the construction sites and factories of the modern world is a remarkable process. Open-pit mining is a highly efficient method for extracting iron ore, followed by extensive processing that transforms raw materials into valuable resources. As the demand for iron and steel continues to grow, the mining industry must balance economic development with environmental responsibility. By adopting sustainable practices, we can ensure that iron ore mining contributes positively to society while preserving the planet for future generations.