Casting, Shaping, and Finishing of Steel: A Comprehensive Overview
Steel, the backbone of modern industries, is a marvel of engineering. From towering skyscrapers to delicate surgical instruments, steel's journey from raw material to finished product involves intricate processes. Among these, the stages of Casting, Shaping, and Finishing (CSF) stand out as vital in transforming molten steel into usable, high-performance products.
π What is CSF in Steel Production?
Casting: Solidifies molten steel into semi-finished forms. Shaping: Refines and molds the steel into desired forms. Finishing: Enhances quality, durability, and usability.
1. Casting: The Foundation of Steel Production
What is Casting?
Casting is the process of pouring molten steel into molds to form semi-finished products like slabs, billets, or blooms. This step determines the steel's structural integrity and is the first step in its journey to becoming a final product.
Popular Methods of Casting
- Ingot Casting
Molten steel is poured into molds and cooled. Suitable for producing large quantities of steel. - Continuous Casting
A modern, efficient process where steel is poured into moving molds. Produces consistent slabs or billets with better surface quality.
Did You Know?
The shift to continuous casting has reduced energy consumption and material waste by 20β30%, making it the preferred method worldwide.
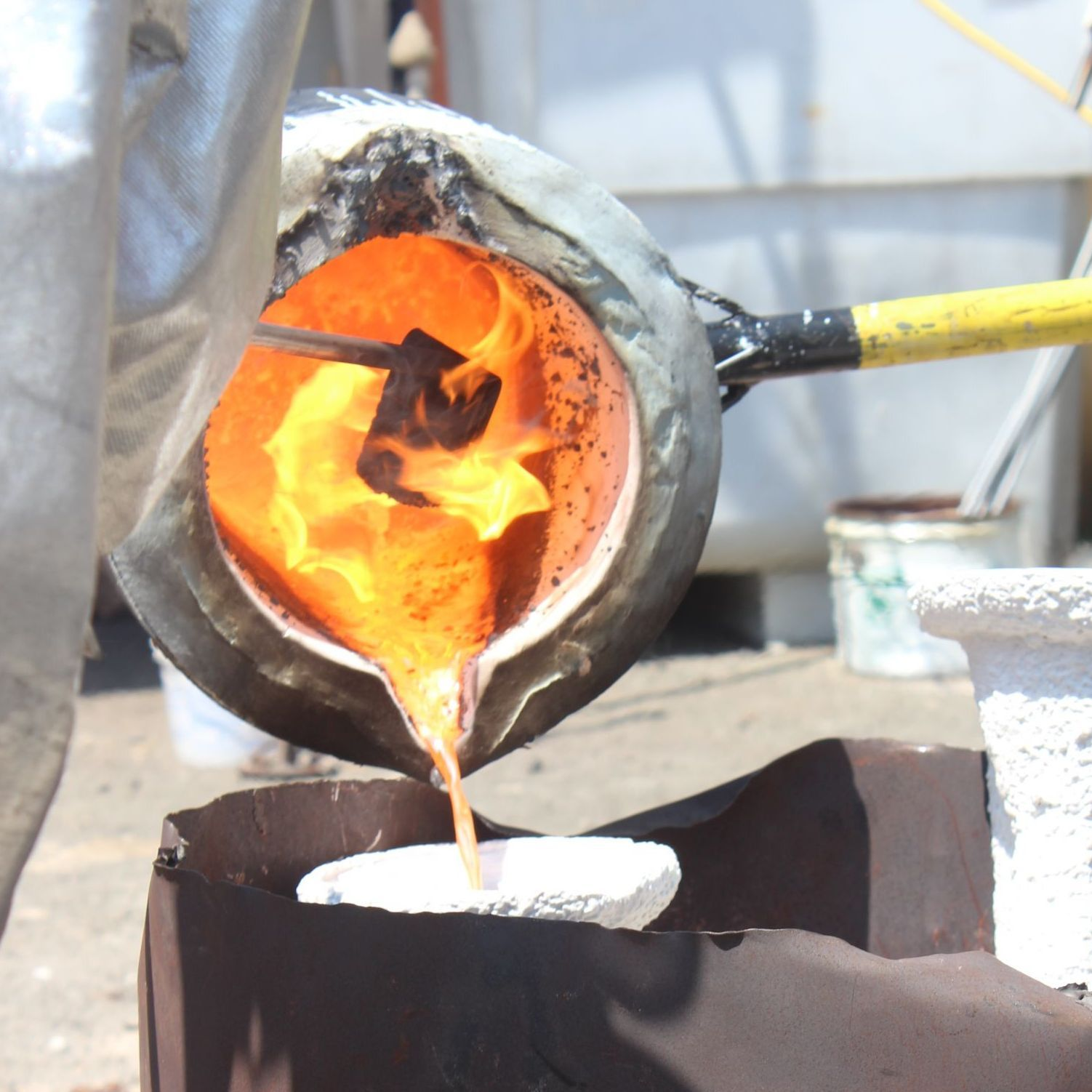
2. Shaping: Molding Steel to Perfection
Once the steel has solidified, it moves to shaping processes, where its physical dimensions and properties are refined.
Key Shaping Techniques
- Rolling
Hot Rolling: Shaping steel at high temperatures for large-scale production. Cold Rolling: Enhances surface finish and strength by shaping steel at room temperature. - Forging
Uses compressive forces to mold steel. Produces durable, high-strength parts like gears and shafts. - Extrusion
Forces steel through a die to create products with fixed cross-sections (e.g., pipes).
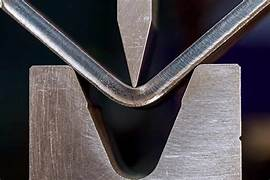
3. Finishing: Perfecting the Final Product
Finishing is where steel gains its final appearance and functionality. This stage ensures the product is ready for specific uses by enhancing its surface, strength, and resistance.
Top Finishing Processes
- Surface Treatments
Pickling: Removes rust and impurities for a clean finish. Coating: Adds protection against corrosion (e.g., galvanization). - Heat Treatment
Annealing: Softens steel for machining. Tempering: Reduces brittleness while maintaining strength. - Cutting and Welding
Laser Cutting: Precision cutting for intricate designs. Welding: Joins steel components for structural applications.
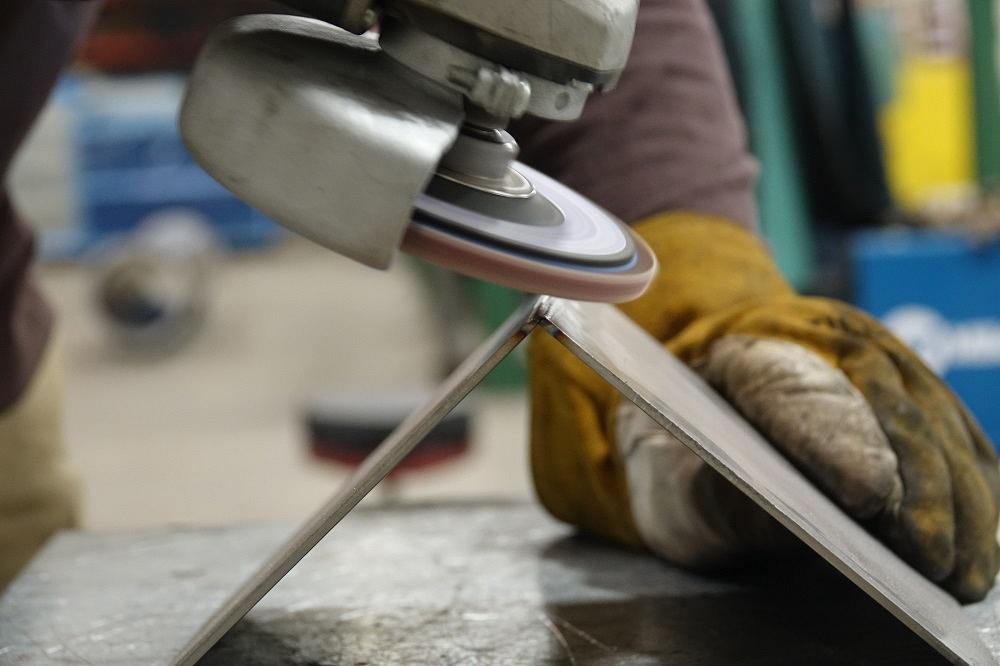
π Why CSF is the Heart of Steel Production
- Customization: Steel products can be tailored to any requirement.
- Durability: Ensures the material withstands mechanical and environmental stresses.
- Cost Efficiency: Reduces waste while maintaining high quality.
π Applications of CSF in Industries
Steel products created through CSF serve a wide range of industries:
- Construction: Beams, bars, and structural components.
- Automotive: Body panels, engine parts, and wheels.
- Energy: Pipes and fittings for oil, gas, and renewable energy projects.
- Aerospace: Lightweight, high-strength parts for aircraft.
- Consumer Goods: Appliances, furniture, and tools.
π Quick FAQs About Casting, Shaping, and Finishing
Q: What is the most common method of casting steel?
A: Continuous casting is the most widely used method due to its efficiency and quality.
Q: Why is cold rolling preferred for precision products?
A: Cold rolling increases steelβs strength and provides a smoother surface finish, ideal for automotive and appliance applications.
π― Conclusion
From molten metal to high-performance materials, the journey of steel through Casting, Shaping, and Finishing (CSF) is a testament to human ingenuity. These processes ensure that steel meets the highest standards of strength, durability, and adaptability.
Explore more about steel production at Sanmarg Steel.