Steel Frame Induction Furnance
Our ET Steel frame melting furnaces are available in capacities ranging from 8mt to 20mt These furnaces are ruggedly built with heavy structural steel for trouble-free operation under harsh melt shop conditions.
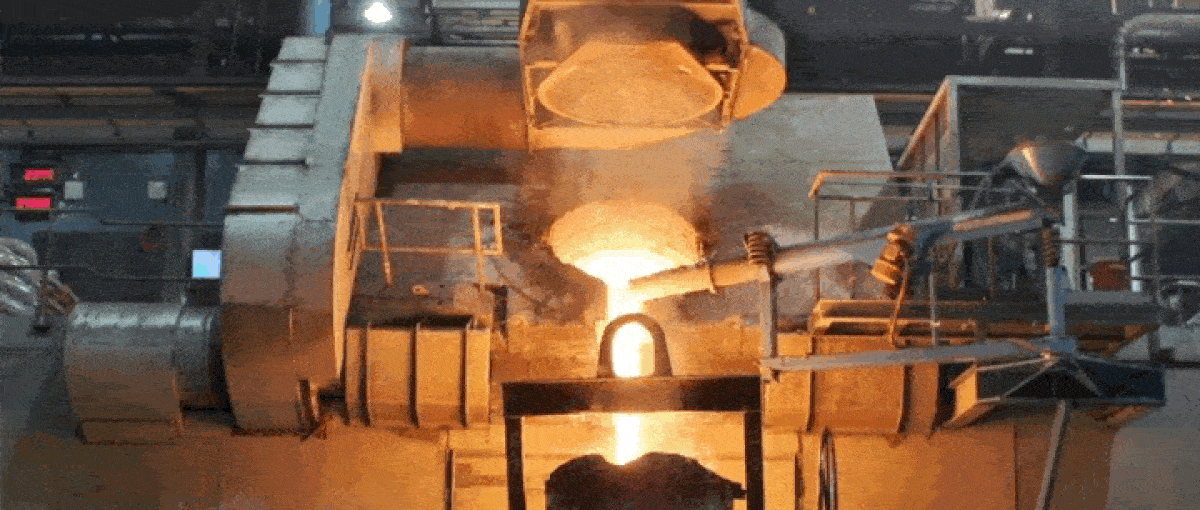
Understanding Steel Frame Induction Furnaces and Electric Arc Furnace Processes
Steel has long been the backbone of industrialization, serving as the fundamental material for construction, manufacturing, and a multitude of other applications. The process of steel production has evolved over the years, with innovations in technology improving efficiency and reducing environmental impacts. Among these advancements are steel frame induction furnaces and electric arc furnaces (EAFs), which play crucial roles in modern steelmaking. This blog post will delve into the characteristics, advantages, and operational processes of these essential technologies.
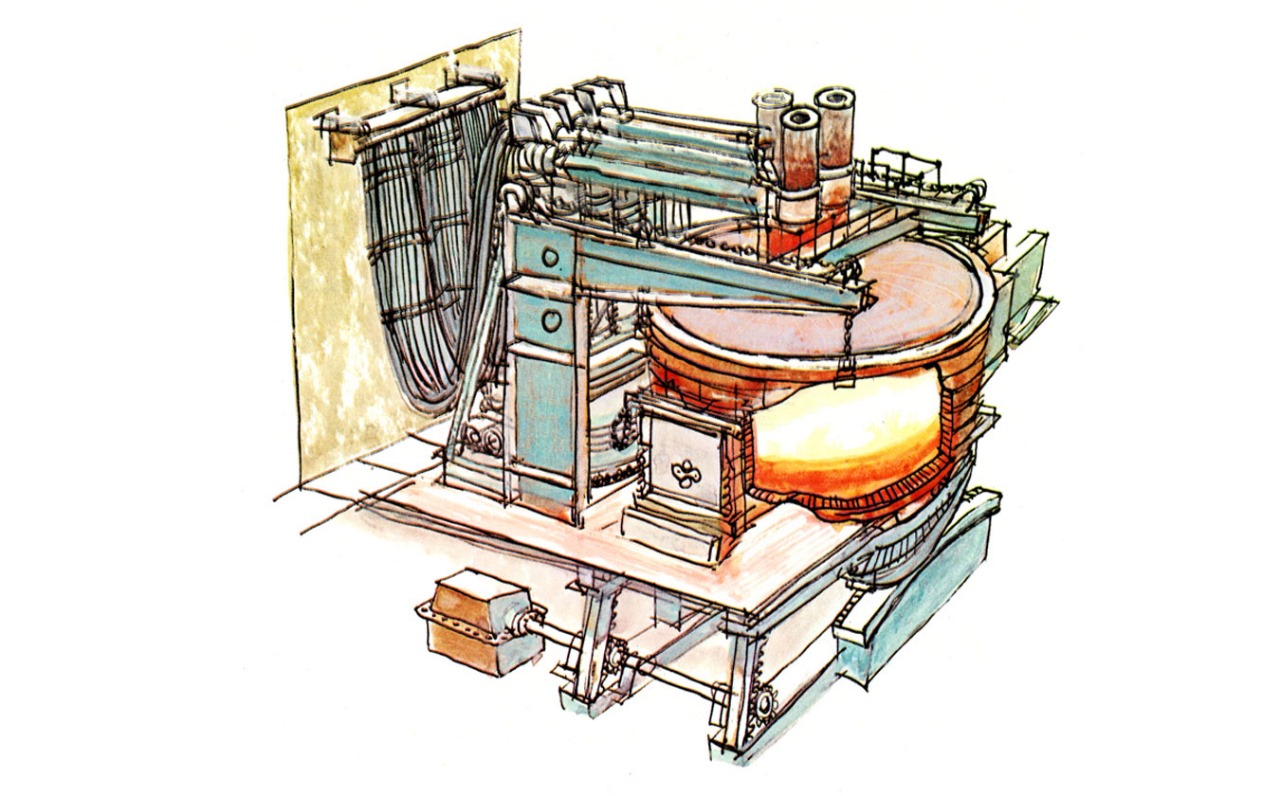
High-temperature furnace or reactor, designed for processes requiring controlled heating and fluid management.
Steel Frame Induction Furnaces: An Overview
Steel frame induction furnaces are essential melting units used in the steelmaking process. They are available in various capacities, typically ranging from 8 metric tons (mt) to 20 mt. These furnaces are specifically designed to withstand the rigors of a melting shop environment, characterized by harsh operational conditions.
Key Features
1. Robust Construction: Made from heavy structural steel, steel frame induction furnaces are built for durability and long-term performance, ensuring trouble-free operation even under challenging conditions.
2. Efficient Coil Design: The use of thick-walled rectangular coil sections minimizes coil losses, enhancing overall coil efficiency. This design contributes to energy savings and increases productivity.
3. Advanced Insulation: Special coil insulation is employed to prevent inter-turn sparking, which can lead to inefficiencies and safety concerns. Additionally, an insulated furnace lid reduces heat loss through radiation, further optimizing energy use.
4. Fume Extraction System: To maintain a safe and clean working environment, steel frame induction furnaces are equipped with fume extraction rings or hoods to capture smoke and fumes generated during the melting process.
5. Coil Support System: Coil supports are designed to maintain an appropriate inter-turn gap and enhance the rigidity of the coil assembly, ensuring operational stability.
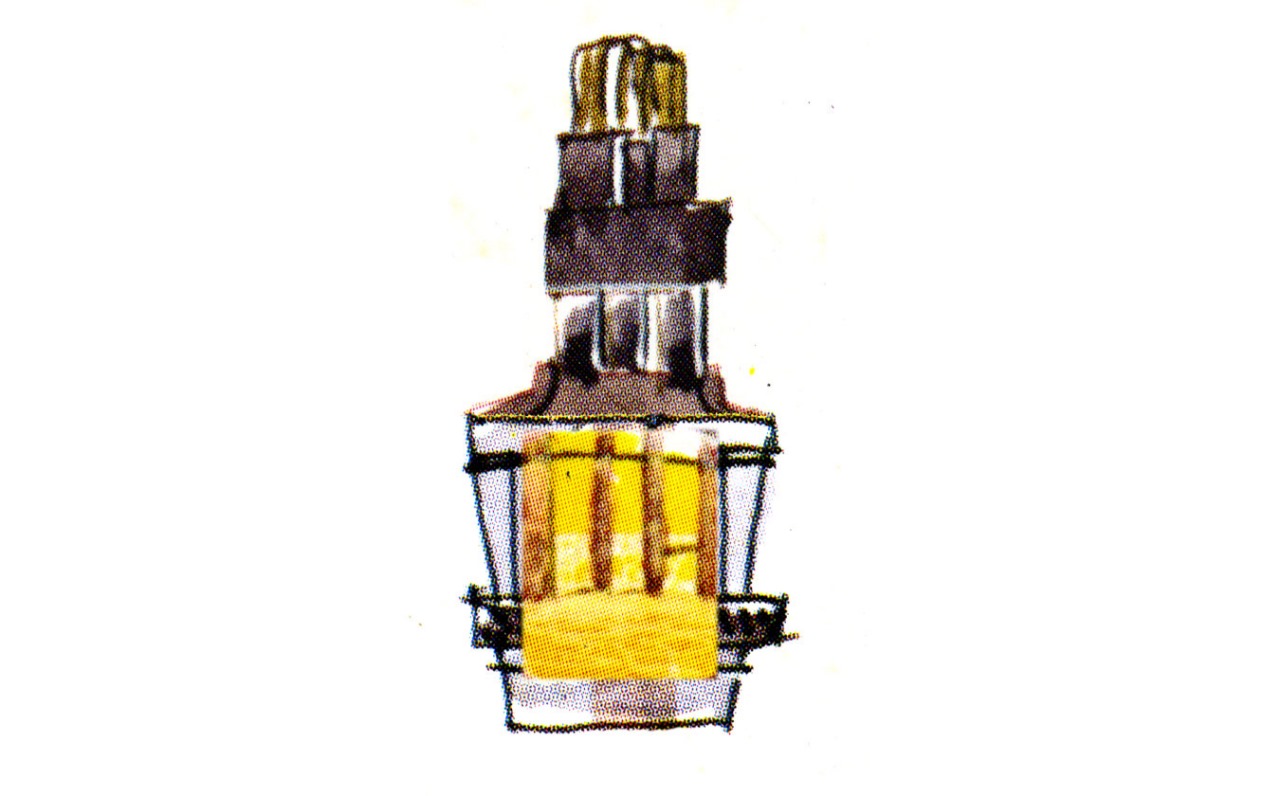
Electric arc furnace
Versatility in Raw Materials
Steel frame induction furnaces can utilize up to 100% scrap as raw material, or various combinations of hot metal, pig iron, Direct Reduced Iron (DRI), and Hot Briquetted Iron (HBI). This versatility allows operators to choose the most cost-effective materials based on market conditions and energy costs.
Electric Arc Furnaces: The Melting Process
Electric arc furnaces (EAFs) represent a revolutionary approach to steel production, relying on electric arcs to generate the intense heat necessary for melting steel scrap and alloy materials.
How Electric Arc Furnaces Work
1. Loading the Charge: The process begins with loading the EAF with a charge, primarily consisting of scrap steel and alloy materials.
2. Generating Heat: Once the charge is in place, a powerful electric current is passed through three carbon rod electrodes inserted into the furnace roof. The current arcs between the electrodes, creating extreme heat that is sufficient to melt the scrap steel.
3. Chemical Reactions: As the charge melts, various chemical reactions occur, transforming the materials into molten steel. This stage is critical for ensuring the desired quality of the final product.
4. Adding Alloys: Once the steel has melted, alloying materials are added to achieve specific mechanical properties and compositions required for various applications.
5. Pouring the Molten Steel: Finally, the EAF is tipped to pour out the molten steel, allowing it to be transferred for further processing.
Advantages of Electric Arc Furnaces
Electric arc furnaces offer several advantages, including:
- Energy Efficiency: EAFs consume less energy compared to traditional blast furnaces, making them more environmentally friendly.
- Flexibility: They can quickly adjust to changes in the type of scrap material used, enabling steel producers to optimize their operations based on material availability and cost.
- Reduced Emissions: The ability to recycle scrap steel reduces the need for raw material extraction, lowering carbon emissions associated with steel production.
Ladle Refining Furnace (LRF): Further Processing
Once the molten steel is tapped from the electric arc furnace, it undergoes further refinement in a Ladle Refining Furnace (LRF). This process is essential for enhancing the quality of the steel by reducing impurities and adjusting its chemical composition.
The LRF Process
1. Tapping into the Ladle: The molten steel is tapped from the EAF and transferred into a ladle, a large vessel designed to hold mol ten metal.
2. Adding Slag: New slag is introduced to the ladle, which acts as a flux to absorb impurities present in the molten steel.
3. Electrode and Argon Injection: A roof containing three graphite electrodes is lowered onto the ladle, and argon gas is injected. This injection creates a stirring motion that facilitates thorough mixing of the steel and slag, enhancing impurity removal.
4. Achieving Specifications: Through careful monitoring and adjustments, the desired chemical composition and temperature of the steel are achieved. This step is critical for meeting customer specifications.
5. Casting the Steel: Once the steel has been refined, it is ready for casting, where it is shaped into various forms for further use.
Conclusion
Steel frame induction furnaces and electric arc furnaces represent significant advancements in the steelmaking industry, offering efficiency, versatility, and environmental benefits. The ability to utilize scrap steel as a primary raw material not only reduces costs but also minimizes the carbon footprint associated with steel production. As technology continues to evolve, these processes will likely play an even more significant role in the future of sustainable steel manufacturing.
Understanding these processes equips stakeholders in the steel industry—manufacturers, engineers, and environmental advocates—with knowledge critical for navigating the modern landscape of steel production. With continued advancements and innovations, the future of steelmaking looks promising, characterized by improved efficiency, reduced emissions, and enhanced quality.